For the drone industry, drone delivery has been an integral part of a larger plan toward a fully integrated UTM system. Yet, achieving this has required a more fluid path toward enabling BVLOS, night flights, and flights over people that has yet to be developed from a regulatory standpoint. For years, the regulations that would enable this has been slow to develop in the United States. Even with the ability to obtain waivers for most of these advanced operations, the regulatory situation still remains mostly restrictive.
Since COVID-19 hit, this discussion has taken on a new urgency. There has been a lot of talk within the industry about how we can utilize drone delivery to aid with social distancing during the pandemic. But, at least in the U.S., this situation has not loosened up regulatory restrictions concerning BVLOS and other necessary regulations.
However, there are ways to legally deploy drones at scale to help with various types of delivery scenarios within visual line of sight. It may not be the autonomous, BVLOS flights the industry wants to see, but these types of flights can help in certain scenarios, such as on hospital campuses or within COVID hot spots. These types of last mile, VLOS and OLOS drone flights are exactly what DroneUp, in collaboration with UPS, the Workhorse Group, and the Virginia Center for Innovative Technology, wanted to test.
A few weeks ago, this team announced that they had successfully completed a series of last mile drone delivery tests within line of sight. In order to find out more about how these tests were conducted, what was learned, what this means for drone delivery, and more, Commercial UAV News spoke to Brendan Stewart, Training Director, and Joe Fuller, CIO, of DroneUp.
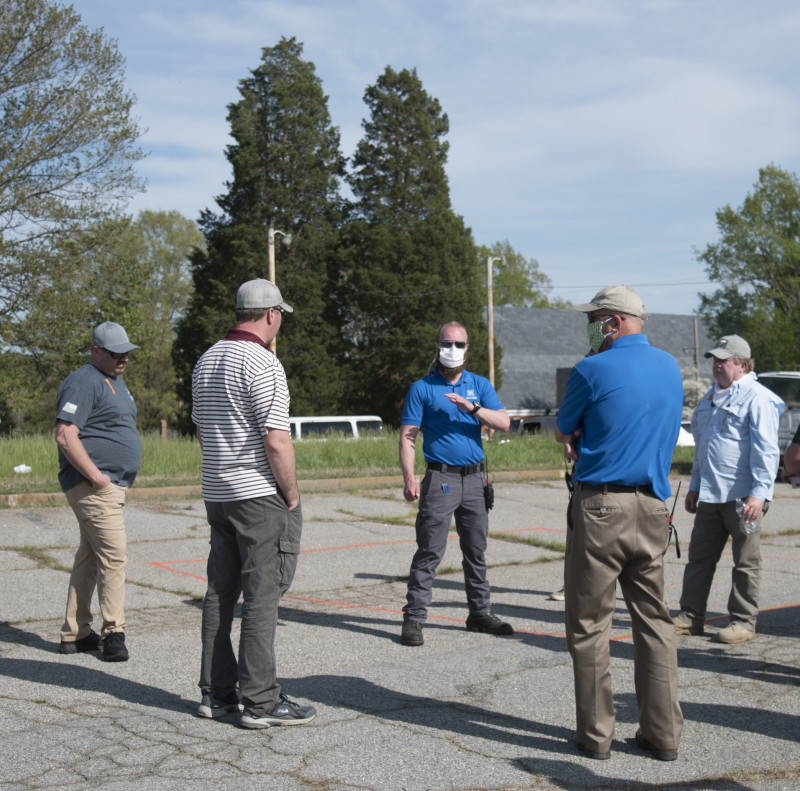
The parameters of this test were very specific. Can you provide a brief overview of what these were and what the objectives of this test were, and why you decided to test these particular aspects of drone delivery?
Brendan Stewart: What we wanted to determine and then validate what our existing capabilities are today, leveraging industry standard equipment on an existing pilot network. The reason for this is that we have a network of pilots nationwide, and what they have access to is industry standard equipment. We wanted to figure out was that, if there were an emergency and we were deployed to deliver medical supplies, how effective could we be with all the existing technology, under the current regulations and available pilots.
We also designed these scenarios to be a lot harder than we would expect to have to accomplish in the real world. For example, if you look at a map of the test site, a lot of those areas included significant hazards. Pilots needed to fly over powerlines, between trees, as all as in and around buildings. In the real world, if you were delivering these supplies, you would probably pick a big open area that would be clear of hazards. But we wanted to determine, if there was a scenario where you couldn’t pre-coordinate takeoff and landing spots or landing areas, could we be effective, even when we turned up the heat and made it more stressful than usual real-world conditions.
What we found was that we really could be. We made 80 of the 81 deliveries successfully. The 81st delivery was a safety abort and the pilot picked up that package and delivered it right back to where it needed to go. This was an overwhelmingly successful test compared to what we had had planned on achieving. It is exciting and it was a lot of fun to be a part of.
What was considered a successful delivery?
Stewart: The drop points were basically a 10-foot radius circle spray painted on the ground. We considered a successful drop and accurate delivery to be anything drop that happened within that 10-foot radius.
Can you talk about how you designed the scenarios for this test?
Stewart: We started with a group of six total test scenarios. Our first scenario was basically a control variable, it happened within line of sight in a test area that required very little hazard mitigation. We then made it progressively more difficult. Test two included areas where the pilot’s line of sight was occluded, and they had to rely on visual observers to guide the pilots over buildings and between obstacles (which is required by regulation). We had some that had to fly between buildings, light poles, and over powerlines, which were very difficult for pilots to make drops on. They were all able to make their deliveries accurately, so we ratcheted up the intensity to make it even harder.
For test three, we wanted to evoke a real-world situation where you have multiple drones, doing multiple deliveries, to multiple locations at the same time. During this test, we needed to deconflict those drones to keep them from being in the same airspace at the same time. We also had to deconflict radio traffic. Each of the drones have a command and control link, so we wanted to verify that they wouldn’t interfere with one another. We also tested automated solutions versus manual deconfliction, we found we had very good performance with both of those solutions.
In test four and test five we tested dynamic hazards. For example, if there was vehicle traffic in the vicinity, could the pilot deal with that? Could the aircraft wait and make a decision to either use a different drop zone, not fly over the vehicle, loiter in place until that vehicle cleared the drone zone and so on. And then finally we tested some of those deliveries at night, because in real world scenarios where you would be responding to an emergency, you don’t have the luxury of only going on bright sunny days, you’re going to have to make deliveries whenever they’re called for.
We had significant successes in all of these tests, even more than what we were planning.
Can you explain what equipment was used, what the payload was, and why they were selected for this test?
Joe Fuller: We used the DJI Inspire 2, which is a drone that many of our database of pilots already own and are operating in the field. We outfitted four of them for the exercises and had a spare. The camera we chose was the Zenmuse X5S. It was a little bit overkill for our purposes, but we wanted to use a camera that would ensure that the pilots had good visibility to do their deliveries, particularly at night. The only problem with that camera was it was a little bit heavy, so it did reduce our payload a bit.
The rated payload for that aircraft is 4,250 grams. We had a 20.4-ounce bag that included bags of sand, a little box, and a medicine bottle with jellybeans in it. We attached this payload to the drone with a Skyzimer, Stork 2, a readily available commercial drop mechanism, which was a simple eight-foot paracord with an S-carabiner connector on both ends.
The way that the mechanism works is that there are two forks ono one side and one fork on the other side attached to the landing gear. Because the Inspire 2 has landing gear that is retractable (so that I can get out of the way of the camera), when the landing gear is raised, those forks separate, and the payload drops. We dropped the payload from a height of two to three feet.
This was useful because, at the time of the exercise, we had been informed that COVID-19 can exist at an approximate altitude of 10 feet—if we didn’t want to get our equipment contaminated, we needed to stay above that 10-foot altitude. Dropping from two to three feet above the ground with an eight-foot paracord meant our equipment was out of harm’s way from virus contamination.
We also found that the eight-foot cord with a bag hanging below it doesn’t produce a negative effect on the air worthiness of the Inspire aircraft. We found a shorter cord created bad harmonic oscillations, but that eight-foot cord was the sweet spot for maintaining stability of the aircraft.
By testing with commercially available gear, we knew that we could marshal a lot of pilots if called on to actually go to a hotspot.
What did this test teach you about last mile drone deliveries? What does this mean for the potential of rolling out drone delivery during this crisis?
Stewart: There is a lot of buzz in the market about fully automating the last mile, and there are huge benefits to that. But there are still two major challenges to fully automating any kind of last mile drone delivery and that is FAA regulation and technology.
Automated drone technology is advancing every day, and that automation is really important to eliminate human factors and streamline workflows. But from what we’ve seen, in order to be successful, you still need a pilot in the loop in these true emergency applications.
For example, one of the areas in which we found that to be really important is in regard to judgement and decision making. We had a test scenario in which the drone had to fly across outside line of sight, you have a pilot in command communicating with a visual observer. That drone had to get over two buildings, drop down between a set of power lines, and make a drop on that 10-foot diameter drop point, while also dealing with a simulated ambulance pulling up to the hospital and driving right into the drop area. Having the ability to recognize that hazard, act dynamically, and make a decision about how to deal with it, while also delivering the payload successfully. It is very difficult to pre-plan for these types of variables, and for that you really need a pilot in the field.
One of the other interesting things that we found is our performance was able to be considerably consistent throughout the operation in terms of delivery time—it was approximately three minutes round trip.
The one area that we found that we need some standardization in is around training and ops. A lot of the pilots in the drone industry are not familiar with radio communications that manned pilots are familiar with. We think there’s some work to do there from the training side. Most drone pilots just don’t have those experiences and if you are running with several drones in the air, I, as air boss, have to act like the drone equivalent of air traffic control. So, I think we can streamline the operation, but overall we were very impressed at how effective we could be with off the shelf technology and the pilots that exist in our network today.
On average we were able to deliver four to five packages per battery charge, depending on wind conditions. For a day of flying, we’re able to be really effective and consistent by rotating those batteries in and out.
What are some safety considerations that you took into account when planning this in order to ensure these kinds of operations are repeatable and safe?
Stewart: I think there are three critical elements from my perspective. First is coming up with a standard operating procedure of how these operations work. There’s no real training program or best practice to do drone delivery operations in an emergency environment at scale—this means we need to establish a standard operating procedure so that everyone is on the same page and speaking the same language. Everyone should also be trained interoperably in those procedures as well.
Second, is having a practical training program and having practical experience. We all know you can get your Part 107 certificate without ever touching a drone. It’s a very steep learning curve to go from passing a written test to here is a drone with an eight-foot tether on it and critical medical supplies—go put that 2,000 feet away in front of a hospital and do that repeatedly for 10 hours a day. That’s not easy. So, we need to develop what that training program looks like to get somebody from zero to hero to be effective in these types of scenarios.
And Third, we need a method on how we can do this to scale. We need to have a scalable command and control solution for managing these flights. We tested a couple of software platforms. One of these platforms allowed us to automate the flights and assign three dimensional corridors to where those flights occur. The other allows for an incident commander on site, which enables that person to see where every drone is on the field; figure out their altitude, their heading, and direction of flight; and assign tasks directly to the pilots. We found that both of these platforms work pretty well. Automated solutions are excellent for getting a pilot right over the target without them having to worry about it, especially at night where situational awareness is going to be limited. But having that ability to have an incident commander that can get on the radio to dynamically direct, reroute, and re-task pilots in the airspace is also incredibly valuable.
Fuller: And just to add to that, another concept we need reinforce is the notion of the sterile cockpit. When a bunch of people are standing around, there is a tendency for chatter but when critical operations are happening, that conversation needs to be kept to mission-critical communication.
We also need to better leverage pre-flight checklists, these are available through most software like DJI, DroneUP, and so on, but we need to establish which checklist we’ll use and then ensure they are used consistently.
And finally, I think another thing to take into consideration is speed limits. When pilots come together, they want to demonstrate their skills and one way to do that is to fly faster than the next guy—nothing happened but ensuring that the payload is kept steady is something to consider moving forward.
What are the next steps for this program and for last mile drone delivery in general?
Fuller: One of the most concise and important deliverables that I’m getting out of this test is being able to put together guidance to anyone who wants to try to do this and the key elements it takes to do deliveries from 500 feet to 2,640 feet (or a half mile). With the scenarios we demonstrated that we can go a half mile round trip—1,320 feet out and 1,320 back—with one visual observer in the field per drone, per delivery. We learned we can effectively manage that flight from beginning to end. I want to publish some guidance that outlines what you are able to do during eight hours of operations, that is you can do X amount of deliveries per hour, you’ll need X number of batteries, and so on. I want to provide that guidance for those different delivery distances. Then if something happens all we’ll need to ask is where can we set up camp and what is the farthest we’ll have to deliver, and then we can tell you how many pounds of stuff we can deliver, how many pilots are needed, how many aircraft you need, how many batteries, and so on. I think we can put something like that together relatively quickly.
What was your overall impression of the last mile drone delivery test?
Stewart: What was really exciting to me about it is that in a very short timeline, we were able to identify a potential need, develop a test method to validate what our capabilities were to meet that need, and then in the midst of a global pandemic, get out in the field and, with all the safety mitigations in place for COVID-19, prove that it works. I think from inception to completion it was less than three weeks’ time, and from my perspective, the speed of development versus the results we had is pretty incredible. We couldn’t have done this without our partners and the collaboration of Lawrenceville, Virginia and those who manage the former St. Paul’s College campus—the cooperation was terrific, they did everything they could to make sure it all went successfully.
Comments