Being able to use drones to create efficiencies is about much more than hardware. The aerial images that drones can gather are absolutely essential when it comes performing a variety of tasks in a faster, cheaper or safer way, but creating efficiencies isn’t merely about capturing information. Automation has and will play a key role in this process, and it’s something that’s already happening in the cell tower inspection industry where automated workflows have proven their potential by helping cut inspection costs by as much as 50%.
Exactly how these efficiencies have been enabled is something that will be explored during the
Benefits of Automated Workflows in the Cell Tower Inspection Industry session at
Commercial UAV Europe by presenters
David Adjiashvili from Drone Harmony and
Sylvain Lotteau from Bentley. The benefits associated with gathering existing infrastructure conditions in 3D to provide a real-world context for design, construction, operations and inspection workflows have been firmly established in a number of different capacities. These efforts have made a positive bottom line impact to projects of all different scales and scopes.
To get a better sense of exactly what that process can look like for anyone interested in unlocking the power of drones cell tower inspection industry, we caught up with David Adjiashvili. We asked him about the factors that help define the 50% reduction in inspection costs, the role regulation plays in adoption for Drone Harmony users, what he’s most looking forward to with the technology and plenty more.
Jeremiah Karpowicz: Do you think drones have the potential to help the cell tower inspection industry more than in any other sector? If so, why?David Adjiashvili: This is definitely one of the markets that can benefit the most, and we’re already seeing those benefits.
First of all, cell site owners are actively looking for ways to cut maintenance costs with their current processes, and they are struggling to do so. They have been experimenting with drone-based inspections and are now looking for company-wide deployment. Secondly, drone hardware and software technologies have matured to the level that the entire inspection process can be streamlined and automated.
Furthermore, cell tower inspections require high-proximity flights around the tower, meaning the flight can be performed in a relatively small area around the tower. This kind of flight eliminates regulatory barriers involved in flying beyond visual line of sight (BVLOS) and in restricted airspace (e.g. above 400 feet).
Finally, the addressable market is huge with 3-4 million towers worldwide. That market is only going to get bigger with 5G adoption. So the benefits in this sector are as evident as they are powerful.
What are some of the factors that go into a calculation of drones being able to reduce inspection costs by as much as 50%?Ultimately, a cell tower inspection with a drone will become a single click operation that we can enable, with minimal risk and a guarantee of high-quality reproducible results. The way we achieve this is by automating the three main steps: data capture, digital model reconstruction and 3D-model based analytics/report generation.
We then streamline all of that into a single seamless workflow. The result is a significantly faster process dramatically reducing the time spent on site, which can be performed by almost any engineer with minimal drone training and with literally no injury risk whatsoever.
The savings are evident when you compare that to traditional inspections which typically mean having a highly skilled engineer climb the tower to visually inspect some components while also collecting imagery to be inspected later on in the office.
Let's break this down into the main cost-saving pieces:
- Less time on site: automated data capture with a drone is faster by an order of magnitude.
- No special training needed: an automated drone inspection can be carried out by any engineer with minimal drone training, as opposed to traditional inspections that require experienced climbers.
- Complete and accurate data: with a drone, it is possible to capture the tower at ultra-high resolution from all angles. This data can be fed into a photogrammetry software system to create a digital model of the tower which can be the basis for a much more complete and in-depth inspection. These models can also be fed into an analytics program for automatic corrosion detection and report generation.
- Huge reduction in risk: climbing towers represents one of the most dangerous jobs in the world.
With the appropriate software components in place, one can expect to enable even more savings in the future when beyond visual line of sight (BVLOS) regulations will allow remote operations.
Why have users struggled so much with issues related to not being able to turn information gathered by a drone into something useful? This is an excellent question for almost any market in the drone inspection domain. As it turns out, very few are the industries where the raw data itself is of any use to the customer, without appropriate post-processing and analytics, and the cell tower industry is no exception.
In a typical flight, a drone will gather hundreds of pictures of the cell site. You can imagine that manually searching through this kind of folder to collect images that are related to something like a specific antenna can be an unpleasant experience. At a minimum, the data gathered needs user-friendly, non-redundant representation. Typically, that’s something that comes in the form of a 3D model that can be visualized recognized and clicked on to prompt images that are relevant to the selected region on the tower.
Taking this a step further, the 3D model can then be used to identify and automatically classify the components on the tower, so that you can do things like detect corrosion and other types of damages. All of that can then be summarized in a nice report. This is what the asset owner is interested in, and that of course goes beyond “data” and is something specifically useful and relevant to that asset owner.
To achieve this kind of a workflow in a cost-effective way, it’s necessary to automate and streamline each one of these steps. The ability to perform each step of the workflow heavily depends on the quality of the result in the previous step. The quality of the data captured directly impacts the quality of the model generated, and the time that is needed to generate. The quality of the model impacts the accuracy of the analytics and quality of the generated reports. Users struggle when they can’t figure out how to effectively transition from one step to the next.
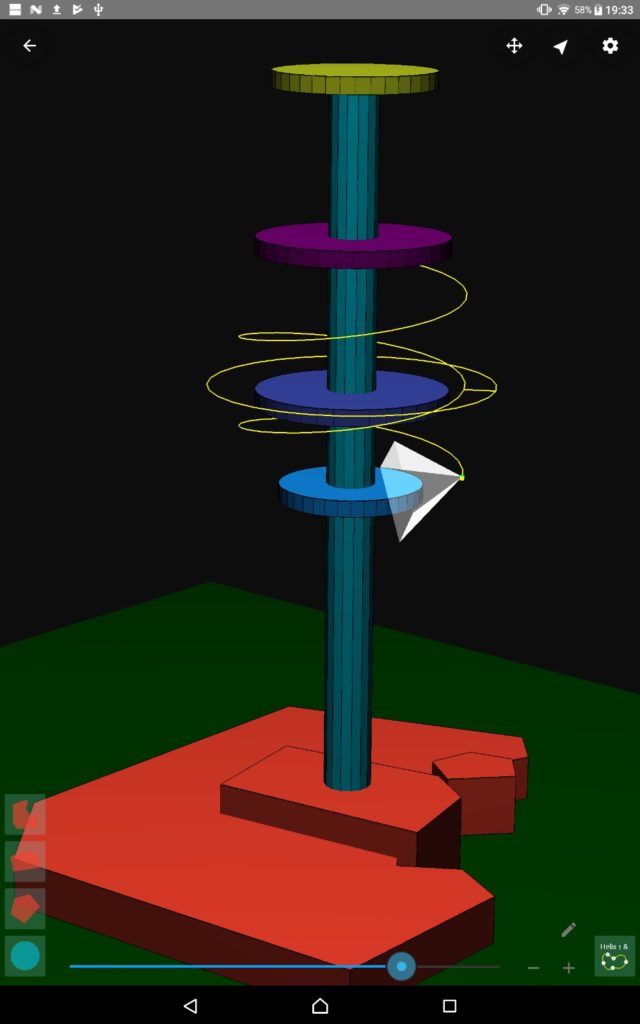
Screenshot of the Drone Harmony app
How has Drone Harmony impacted issues related to the way in which data can be gathered and utilized at a cell tower?Drone Harmony's Cell Tower Scan is the first application designed solely for the task of capturing data at cell sites with a drone.
In a nutshell, we have made it as easy as possible for the pilot to obtain the quality data that is needed. The flight plans in Drone Harmony are generated automatically and are tailored to a rough 3D model of the inspected tower. The model can be either imported or easily constructed in the application, using a simple wizard. Obstacles can also be included in the model and the generated plans avoid these obstacles automatically. Every step of the simple setup procedure is visualized in 3D, so there is very little uncertainty or room for error. Finally, the app flies the drone automatically.
Cell Tower Scan is designed to replace a process that sees someone manually flying the drone, or manually planning a flight path by placing waypoints in a 2D interface. We have developed Cell Tower Scan in close collaboration with Bentley's Reality Modeling team to guarantee that the data captured by the app is ideal for Reality Modeling and 3D reconstruction. We have also worked directly with pilots and clients to guarantee that the end-to-end solution delivers both the required quality of results and that we achieve our cost saving targets.
What kind of a learning curve is associated with the solution?From our experience, pilots with even basic skills and knowledge are able to use the application independently after at most 30 minutes of training. Pilots with more experience with flight planning software are often able to learn it themselves in the same time.
Have your users struggled with regulatory challenges related to utilizing the automated capabilities of your solution? The regulatory barrier for cell tower inspection is relatively low, as it typically does not require beyond visual line of sight (BVLOS) operations or flight above 400 feet. From our experience, most companies that are contracted to perform such work are able to easily acquire the needed permissions.
What has you excited about the future of drones and how they might redefine what it means to gather and utilize information for cell tower inspections? I'm excited about how this technology can simultaneously solve several pain points for an industry that is ready for its adoption at scale. With 5G becoming the next standard in the industry leading to a vast increase in the cell sites, these pain points are only projected to increase, so the timing is perfect.
Ultimately, I'm hoping that this success story will encourage decision makers in other industries to break out of the pilot project philosophy for drone technology and lead to at-scale business-wide adoption.
To hear more about how Drone Harmony has been able to use this technology to reduce inspection costs by as much as 50%, hear David present during the Benefits of Automated Workflows in the Cell Tower Inspection Industry session at Commercial UAV Expo Europe.
Comments