AirShaper CEO Wouter Remmerie is committed to addressing issues around the aerodynamics of a variety of vehicles, including uncrewed aerial vehicles. His Belgium-based firm has worked with clients in the drone, aviation, and air taxi industries to improve aerodynamic efficiency, boost performance, and increase profitability. Central to their work is aerodynamic testing, including the use of Computational Fluid Dynamics (CFD).
Recently, Commercial UAV News spoke with Remmerie about his company’s approach to aerodynamic testing and how UAV clients benefit from AirShaper’s efforts.
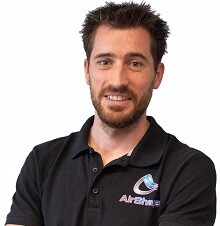
Commercial UAV News: Explain the issues around aerodynamicswith commercial drones.
Remmerie: When you start from scratch, you often start with generally available building blocks, such as batteries, drones, and structures, because it's simply very hard to design everything in a custom way.
Those individual components are often very good, but the best performance is usually found when all of them are tuned to each other. To help identify these issues, AirShaper runs aerodynamic simulations. These simulations can lead to design improvements and better performance.
Commercial UAV News: Describe your work with senseFly. What challenges were they seeking to overcome and what processes were used to help them?
Remmerie: senseFly was looking to improve the efficiency of their eBee Classic, an existing drone which had already a "winglet" or an upright part at the end of the wing to reduce the wing tip vortex. As the drone is used for terrain mapping, every extra minute it can stay in the air increases the profitability.
So, as a starting point, we first analyzed that drone using our simulation platform. We were pitched against two other software solutions, and our results were the most satisfactory—also compared to wind tunnel tests they had already performed. Once we had this "virtual simulation reference," we jointly looked at how we could improve the design by understanding the vortex structures around the wingtips. We analyzed various variations of the wingtip, including one which featured both an upper and lower wingtip.
This one proved to be the most efficient for their specific fixed wing drone. Actual field tests showed a 30% improvement in lift/drag ratio—the main efficiency indicator for aerodynamics of lifting bodies. That means they can fly for 30% longer on the same battery charge or reduce battery size and cost by roughly 30% for an identical flight time.
Commercial UAV News: Describe some of the problems associated with CFD simulations and explain how AirShaper has automated and improved the process.
Remmerie: Running a CFD simulation typically involves a number of steps. The steps include fixing the 3D geometry, which can take days or weeks, setting up the boundary conditions, or creating the right size for the "virtual wind tunnel" around the drone, and creating the mesh or the 3D computational grid.
Going through these steps is typically an iterative process to find the right settings for the simulation. Such simulation is usually done on proprietary hardware, which means you need to schedule it, secure a license, store/transfer the data afterwards. CFD simulations also involve monitoring key parameters like the residuals, forces, and moments to determine when it has finished. It also includes post-processing. Once a simulation is done, you need to convert the raw data into key performance figures, like lift and drag values, pitch roll, and yaw moments, as well as visualizations, such as pressure values on the surface and streamlines around the object.
At AirShaper, we've automated that entire sequence. A user can set up a project in literally just five minutes and get the full report back in just a few hours and analyze the 3D results online.
Once a simulation is done, users can choose to interpret the results themselves or ask AirShaper for consultancy on how to also redesign the drone and optionally run another simulation to see the effects. For further performance improvements, users can also let the AirShaper algorithm automatically improve their design through a process involving AirShaper’s Aerodynamic Shape Optimization. In this case, the software will automatically morph the 3D model to improve the aerodynamic performance.
Commercial UAV News: What’s next for AirShaper? What other projects you are working on that will improve performance and efficiency in the drone space?
Remmerie: Among the projects we’re currently working on include adding propellers to a full drone simulation. In this case, we take the propeller effects on the overall airflow around the drone into account.
We are also working on stand-alone propeller analysis. In this case, we're working together with propeller manufacturers to develop a stand-alone simulation tool for propellers. The goal is to provide tools to improve the efficiency and thrust and to lower the noise. This is especially important as drones and air taxis get closer to "human spaces."
Comments