Lidar emits light actively and outputs “point cloud” images with the received reflected light, outlining the details of all road objects with a complete representation of the 3D world. Lidar plays a critical role in drone construction, establishing itself as an indispensable sensor for an Unmanned Aerial Vehicle (UAV). With lidar, UAVs not only free up time for humans but also offer solutions to problems such as covering vast areas in a shorter period of time, navigating tighter spaces, and protecting humans from unsanitary locations. So how does our lidar navigate diverse challenges, cater to the perception needs of robotic applications, accelerate the adoption of unmanned technology, and enhance safety and production efficiency?
Lidar’s robust sensing ability enables accurate recognition of hazards such as dust, raindrops, and snowflakes. It reduces the likelihood of false alarms triggered by small obstacles and enhances the overall safety of UAVs. With multiple-return technology to process returned signals, lidar corrects the data it receives, enabling laser beams to partially penetrate through rain, snow, fog, haze, and dust—thus dealing with the challenges of extreme climates. Meanwhile, lidar that passes reliability tests, including vibration and weather tests, can endure the vibration of the vehicle and remain functional in harsh weather environments. To achieve large-scale droning operations, without human intervention, companies choose lidar as the primary sensor in their sensor fusion approaches, which effectively addresses the huge demands of area imaging.
Thanks to lidar’s extensive detection range, high resolution, and strong anti-interference capability, it can achieve exceptional precision in detecting and identifying objects. Even with its perception, it never compromises or detects details such as identifiable characteristics, as lidar is hardware only. Further processing comes from secondary software from a different company. For large-scale droning areas, this plays a significant role in the choice to use lidar in comparison to cameras.
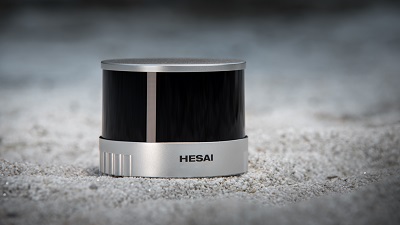
Lidar is a core component of the perception system regardless of the scenario. Hesai's XT series lidar was made specifically for the robotics and unmanned vehicles industry. The XT series demonstrates exceptional qualities with its high precision, minimum range of zero, exceptional reliability, and affordability. These advantages perfectly cater to the perception needs of unmanned vehicles across a wide range of scenarios.
- High precision helps the UAV “see clearly” with a maximum ranging accuracy (1σ) of 5 mm, a maximum distance of 300 m, 1cm precision or better on most targets, and an outstanding Probability of Detection (PoD) exceeding 90%, outperforming its competitive products in the market. This attention to detail enhances our point cloud accuracy, capturing low-reflective objects.
- A minimum range of zero helps the UAV to “see completely”. This function is made possible through Hesai’s innovative optical transceiver design and accurate assembly and adjustment. As a result, UAVs equipped with XT series lidar can detect objects in both near-fields and far-fields with unparalleled accuracy.
- High reliability helps UAV companies decrease costs and increase benefits. Passing dozens of reliability tests such as vibration, drop, temperature, humidity, aging, and electrical, the XT series offers unmatched stability. With a designed lifetime exceeding 30,000 hours under typical working conditions, it substantially lowers the risks of product failure and maintenance costs.
Underpinned by XT series, lidar has achieved regular operations in numerous countries worldwide. With the large-scale adoption of UAVs, the lidar market led by Hesai’s XT series is positioned for continuous and rapid expansion in the future, further advancing UAVs in more applications.
Comments